A hot mix asphalt plant operation is a very simple and effective method for producing asphalt. There are several benefits to starting a hot mix asphalt plant operation. First, they are environmentally friendly. Hot-mix methods do not involve the use of chemicals or other harmful solvents, which makes them ideal for both the environment and the people working in them. Using hot mix asphalt also reduces the amount of clay soil that is produced during the mixing process, thereby cutting down on the amount of waste that is left behind after the asphalt has been poured. Lastly, asphalt hot mixes can be mixed using a large compressor that is relatively easy to maintain.
The basic recipe for making an asphalt hot mix(mezcla de asfalto caliente) is cement, sand, water, and fertilizer. The mixture of these three ingredients will be heated so it can expand into the proper shape for the asphalt. It is important to allow the mixture to cool before the mixing starts, which is why there is a need to have a high heat-resistant cement. Once the cement is ready, it should be watered down and then allowed to set so it can achieve its rigid shape. It is best to mix the cement two to three days before the actual pouring of the asphalt so it can properly set.
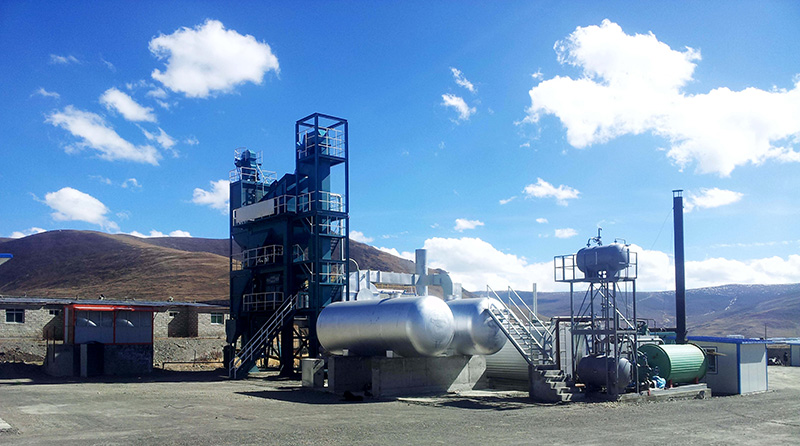
Before any other ingredients are added to the hot mix, the pre-composted gravel is put into the rear feeder on the mixing truck. This gravel is an important part of the composting process because it is what makes it soft enough to mix with the ingredients of the asphalt. Once the gravel has been added, it is just a matter of turning the truck on and pouring the hot mix into the back of the truck.
While there are several hot mix asphalt plants operating throughout the country, the largest operation is located in Livermore, California. It is run by Bob Johnson. He spends about six months out of the year at his facility mixing and tamping asphalt. The rest of the year, he works out of his home. To make his business successful, he has a large staff that works around the clock to complete the job as soon as possible.
The process that the hot mixer goes through to turn the raw ingredients(materias primas) into a final product is quite fascinating. When the ingredients reach the end of their journey, they are first sprayed with an anti-freeze. Then, the feed roller and the agitator pumps are used to flatten out the mixture. The mix is then passed through a cooling chamber where it sits while it cools. This allows the asphalt to cure and harden while providing the asphalt plant with just the right amount of heat for a safe and effective filling.
With the help of a pre-mixer and an automatic grinding machine, hot mix asphalt plants are able to make asphalt that ranges from one inch to twelve inches thick. At its minimum, it is the product of many hours’ worth of mixing, spiking, cooling, and tamping processes. In its prime, the product is thick enough to provide a durable, flexible layer of asphalt that can be used for driveways and walkways. It also enables repair crews to set up a temporary foundation on the site of the construction. When properly mixed and pre-cured, asphalt acts like a highly flexible rubber, which means that any damage that is caused to the pavement, such as chipping or gouging, will not be noticeable.
As technology increases, hot mix asphalt products are becoming more widely available. In addition, because there is no need to wait for long periods of time to let the asphalt cure, the operation can be done on a smaller scale than traditional construction methods(métodos de construcción). While it takes more manpower and a bit more money to start up an asphalt plant than conventional construction methods, it can provide a lucrative return on investment in a shorter period of time. Therefore, it is no wonder that many local municipalities and state regulatory agencies are encouraging the growth and expansion of this innovative and beneficial industry.
The demand for hot mix asphalt has created a variety of job opportunities for asphalt manufacturing plants. Since the asphalt is typically thicker than standard asphalt, these plants must create custom sizes in order to meet the needs of construction and pavement companies. In addition, since the mixing and preparation must occur in a controlled environment, many companies choose to outsource their asphalt manufacturing and hot mix plants to a company that specializes in this field. By outsourcing to a specialized manufacturer, companies free up their own personnel to handle other pertinent matters in the business or for marketing purposes. While some areas may require one or two plants to meet the demand for asphalt, other regions can have as many as ten or eleven plants operating at one time, depending on the number of companies that choose to outsource the production. When you want to install a hot mix asphalt plant, AIMIX can give you high quality equipments.